Oak flooring is renowned for its timeless beauty, durability, and versatility, making it a popular choice for both traditional and modern homes. The rich textures and natural grains of oak add a touch of elegance to any space, enhancing its aesthetic appeal.
However, before investing, it’s crucial to understand the various factors that can impact the overall cost of oak flooring. This comprehensive list aims to provide you with detailed insights into these factors, helping you make an informed decision and ensuring you get the best value for your money.
Understanding cost factors is essential not only for budgeting purposes but also for ensuring that the oak flooring chosen meets both your design preferences and functional needs.
1. Type of Oak
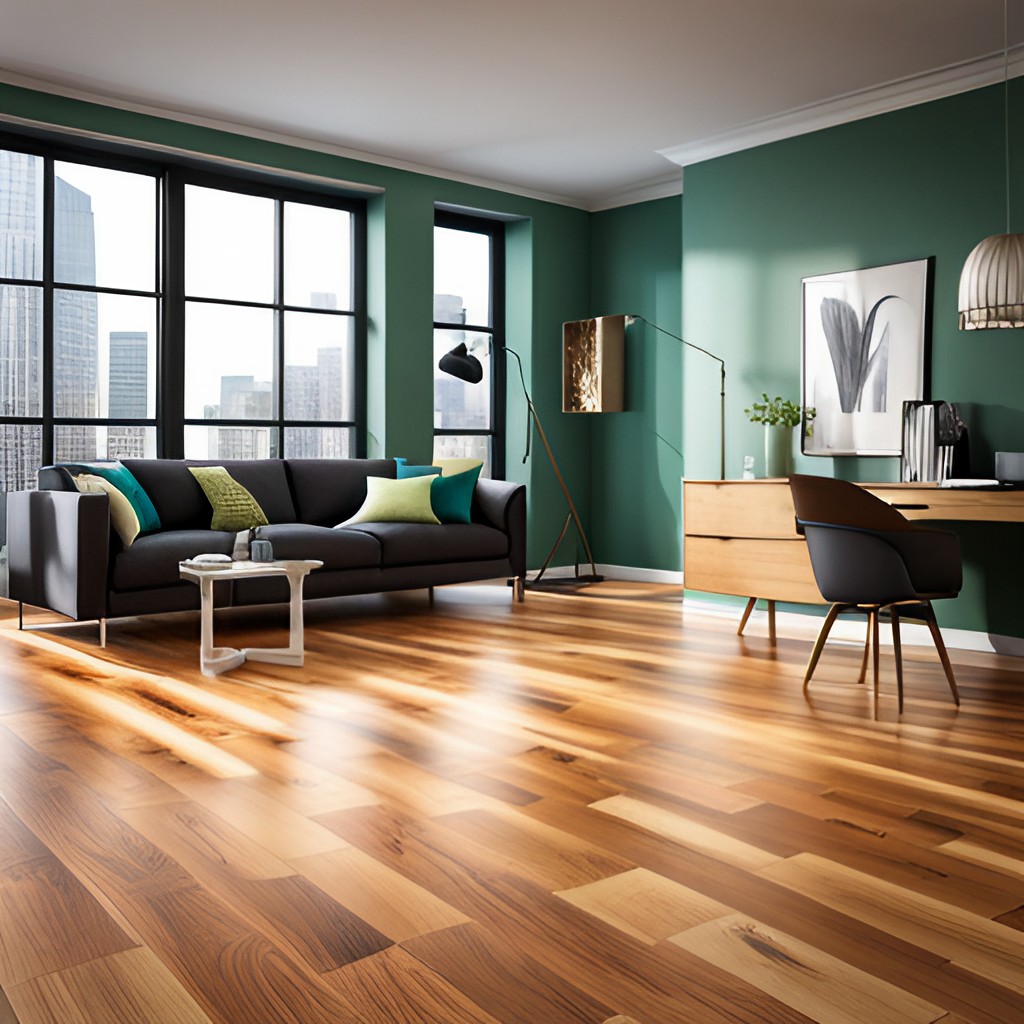
Differences between Red and White Oak
When selecting oak flooring, it’s important to consider the differences between red and white oak, as they can significantly influence the appearance, durability, and cost of your flooring.
Red oak is known for its warm tones and prominent grain patterns, which can range from light reddish-pink hues to deeper amber shades. It tends to be slightly softer than white oak, making it more susceptible to dents and scratches, but it’s still a durable option overall.
White oak, on the other hand, generally features cooler, more subdued shades, such as light brown to grayish hues, and exhibits a tighter, more uniform grain pattern. This type of oak is harder and more resistant to moisture, making it a suitable choice for areas with higher humidity levels.
The distinct characteristics of red and white oak not only affect their aesthetic appeal but also their long-term performance and maintenance needs, which should be carefully considered when planning your flooring project.
Cost Implications of Each Type
The cost of oak flooring can vary significantly between red and white oak due to their differing characteristics and market demand. Red oak, being more abundant in supply, generally tends to be more affordable than white oak.
Its popularity and availability make it a cost-effective choice for homeowners looking for a budget-friendly option that still offers a beautiful and durable surface.
Conversely, white oak, with its higher resistance to moisture and more subtle grain, is often priced at a premium. This higher cost reflects its desirable qualities, including enhanced durability and suitability for a wider range of environments.
When deciding between red and white oak, it’s essential to weigh these cost implications against the specific needs and conditions of your project to ensure you make an economically sound choice.
2. Grade of Oak
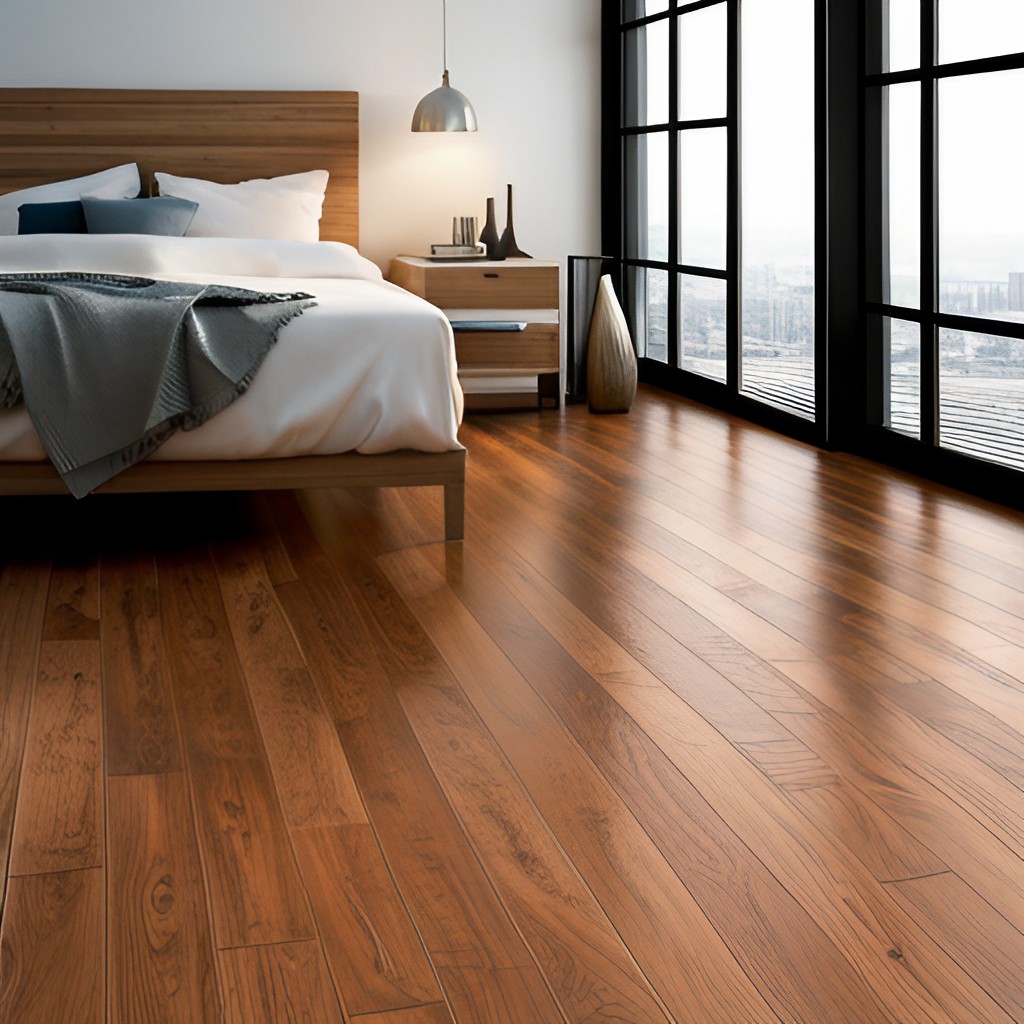
Explanation of Various Grades
Oak flooring is typically categorized into several grades, each indicating the quality and appearance of the wood. The primary grades include Clear, Select, Number 1 Common, and Number 2 Common.
Clear-grade oak is the highest quality, exhibiting minimal defects and a uniform grain pattern, making it ideal for a smooth and polished look. Select grade follows, featuring slight variations and minor natural characteristics such as small knots.
Number 1 Common grade includes more pronounced marks and variances, providing a more rustic and natural appearance.
Finally, Number 2 Common grade, also known as Cabin grade, has the most pronounced imperfections, including larger knots and color variations, offering a rugged and unique charm.
How Grade Affects Price
The grade of oak flooring significantly influences its cost, with higher grades commanding higher prices due to their superior quality and aesthetic appeal. Clear-grade oak is the most expensive, reflecting its pristine nature and rarity.
Select grade, while slightly less costly, still carries a premium price due to its high quality and refined appearance. Number 1 Common grade is more budget-friendly, offering a balance between quality and cost with its charming, rustic look.
Number 2 Common grade is the most economical option, appealing to those who embrace a more natural and varied aesthetic at a lower price point.
When selecting oak flooring, it’s crucial to consider how the grade aligns with both your aesthetic preferences and budget constraints.
3. Plank Size
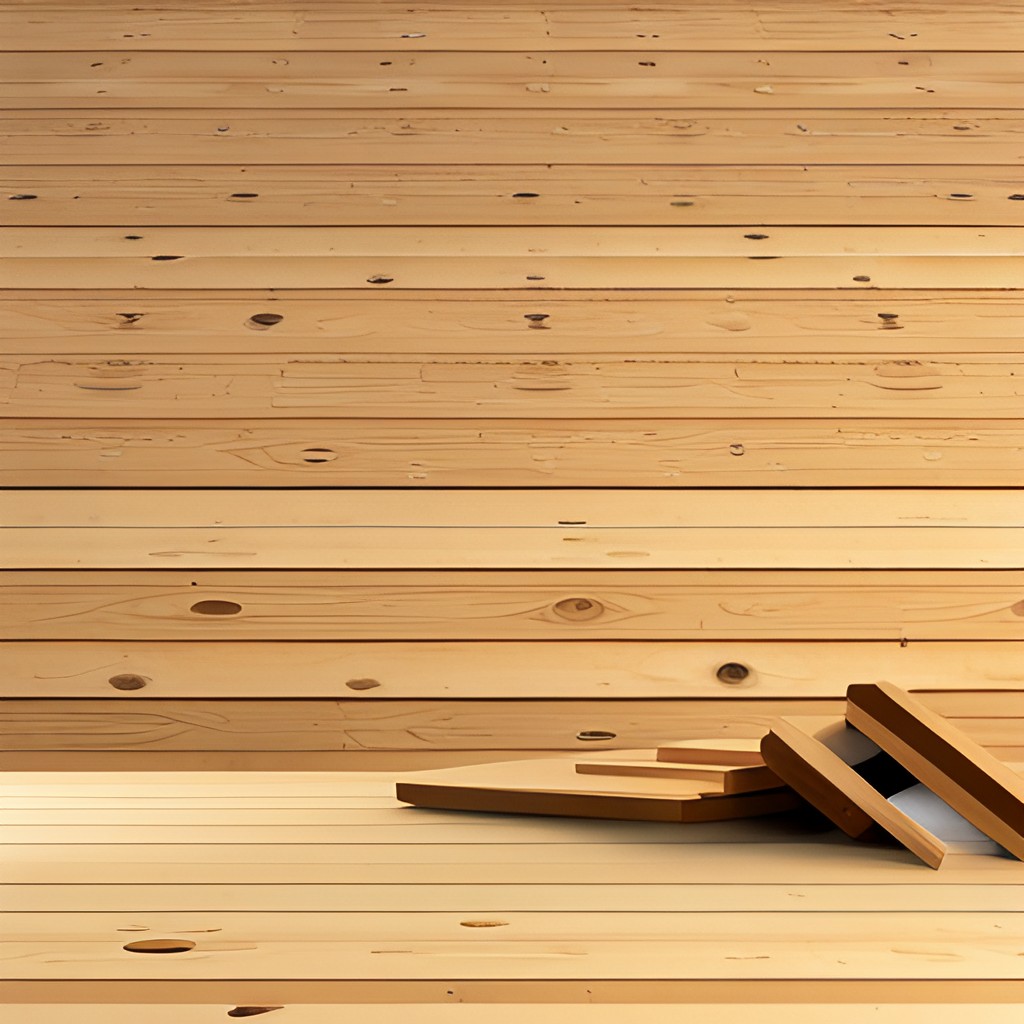
Width Considerations
When choosing oak flooring, the width of the planks plays a crucial role in the final appearance of the space. Narrow planks, typically measuring between 2 1/4 to 3 inches, offer a traditional and classic look, ideal for smaller rooms as they can make the space appear larger.
Wide planks, ranging from 5 inches and broader, create a more contemporary and spacious feel, perfect for larger areas where the wider boards can showcase the rich grain patterns of oak.
However, wider planks can be more prone to expansion and contraction with changes in humidity, potentially impacting their longevity in certain environments.
Length Considerations
The length of the oak planks also affects the visual appeal and installation process. Longer planks, which can range from 3 to 7 feet or more, provide a more seamless and unified look with fewer joints, enhancing the overall fluidity of the floor.
Shorter planks, often varying between 1 to 3 feet, offer a more dynamic and varied appearance, which can add a unique character to the floor, but may result in more visible seams.
The choice of plank length depends on the desired aesthetic as well as practical considerations such as room size and installation complexity.
Impact on Overall Cost
Both the width and length of oak planks can significantly impact the overall cost of the flooring project. Wider planks typically come at a higher price due to the increased amount of raw wood required and the additional processing needed to ensure stability.
Similarly, longer planks tend to be more expensive because they are more challenging to source and manufacture without defects.
Therefore, while wider and longer planks can provide a more luxurious and cohesive look, they will also increase the overall expense.
4. Finish Options
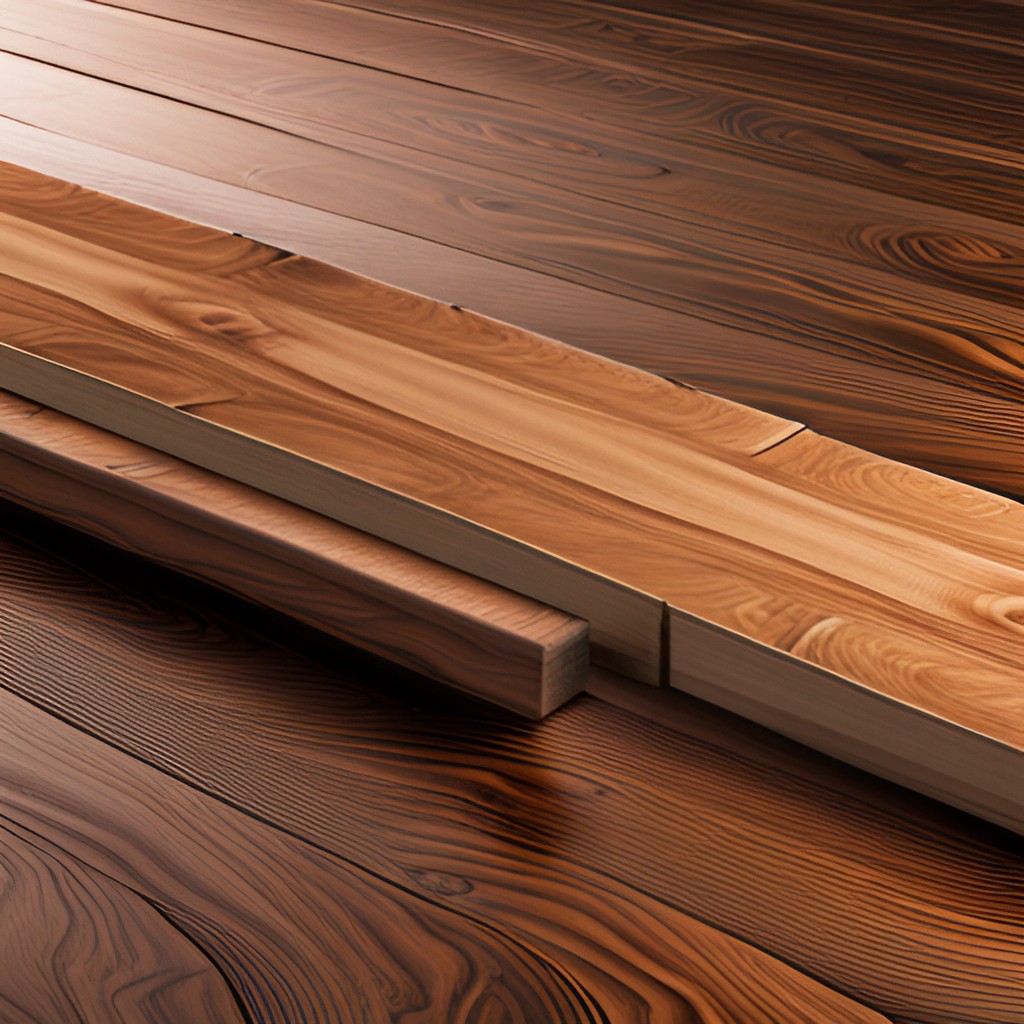
Types of Finishes Available
When it comes to finishing oak flooring, there are two primary options: unfinished and prefinished planks. Unfinished planks allow for a high degree of customization because they can be sanded and stained on-site to match specific decor needs.
This option provides the flexibility to choose any color or finish, but it requires more time and labor for installation and finishing on-site.
On the other hand, prefinished planks come with a factory-applied finish, which ensures a high-quality, consistent look and a quicker installation process. Prefinished floors often include protective layers that extend the floor’s longevity, making them a convenient and durable choice.
Cost Differences Between Finishes
The cost differences between unfinished and prefinished oak planks can be significant. Unfinished planks are generally less expensive upfront but require additional labor and materials for the on-site finishing process, which can increase the overall cost.
This includes expenses for sanding, staining, and applying protective coatings, as well as extended installation time. Prefinished planks, though more expensive initially, can be more cost-effective in the long run.
The factory-applied finish reduces installation time and minimizes labor costs, it generally results in a more durable finish that may reduce long-term maintenance expenses.
5. Installation Method
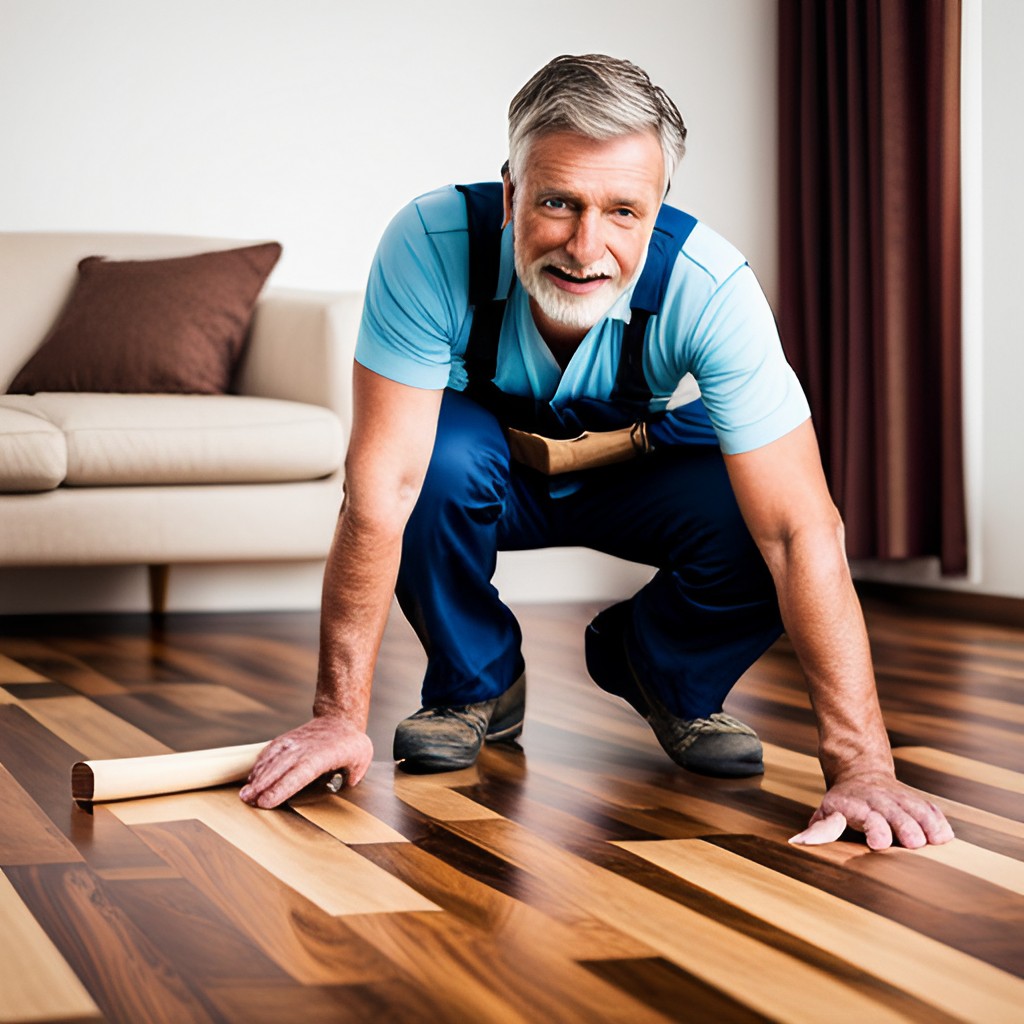
Labor costs can vary significantly depending on the installation method used. The nail-down method is typically the most labor-intensive, resulting in higher labor costs. It requires meticulous preparation and precise installation, often necessitating professional expertise.
The glue-down method also incurs moderate to high labor costs due to the need for careful application of adhesive and proper placement of planks.
The floating method, being simpler and faster, usually results in the lowest labor costs among the three options.
The choice of installation method can greatly impact the overall cost of oak flooring. While the nail-down and glue-down methods may offer superior stability and durability, their higher labor and material costs can increase the total expense.
Conversely, the floating method, with its lower labor costs and quicker installation time, can be more cost-effective initially but may require more frequent maintenance.
When budgeting for oak flooring, it is essential to consider both the immediate and long-term costs associated with each installation method to make an informed decision.
6. Subfloor Preparation
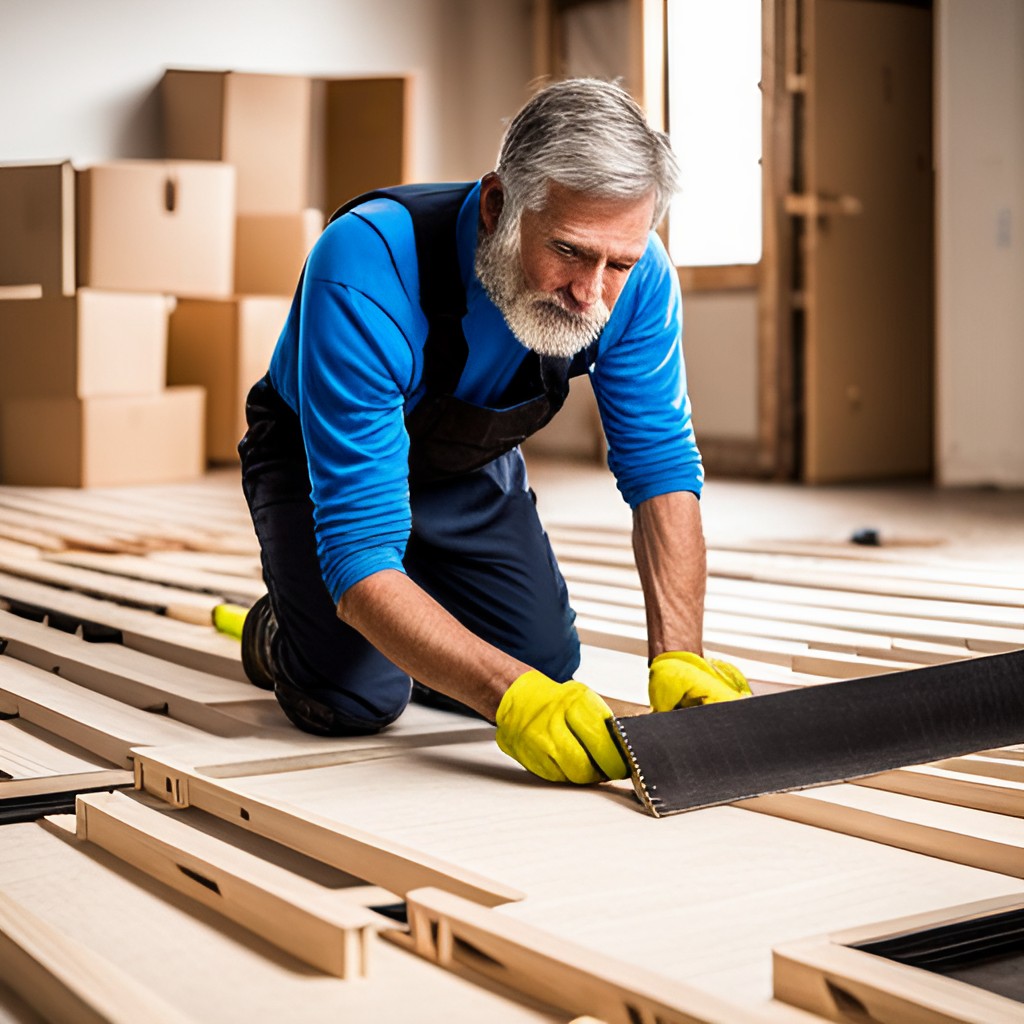
Proper subfloor preparation is a critical step in ensuring the success and longevity of oak flooring installation. The necessity of preparing the subfloor cannot be overstated, as it directly impacts the final appearance and durability of the flooring.
Subfloor preparation can include a variety of steps such as leveling the existing subfloor, removing old flooring materials, and addressing any moisture issues.
Each of these processes can add to the overall cost of the project.
Leveling the subfloor is often necessary to create a smooth and even surface for the oak flooring. Uneven subfloors can result in gaps, squeaks, and other issues that compromise the integrity of the floor.
The cost for leveling can vary widely depending on the existing condition of the subfloor and the amount of work required. Removing old flooring materials, such as carpet, tiles, or existing wood flooring, can also incur significant labor and disposal costs.
Additionally, if moisture problems such as leaks or mold are detected, they must be addressed before installation, often leading to extra charges for repairs or treatments.
The potential additional charges associated with subfloor preparation can have a substantial impact on the total cost of oak flooring. These factors should be carefully considered during the planning and budgeting stages of the project.
Properly prepared subfloors contribute to a more durable and aesthetically pleasing installation, potentially saving on long-term maintenance and repairs. By accounting for these preparatory steps, homeowners can make a more informed decision regarding the overall investment required for their oak flooring project.
Related Topics:
7. Regional Price Variations
Geography plays a significant role in determining the material and labor costs associated with oak flooring projects. Various factors such as local availability of raw materials, regional wage rates, and transportation costs contribute to price discrepancies across different areas.
In regions where oak trees are abundant, the cost of oak hardwood may be lower due to reduced transportation costs and the availability of local sawmills.
For example, states like Wisconsin and Missouri, which have substantial oak tree populations, might offer more competitive prices for oak flooring materials compared to areas where oak is less common.
Labor costs also vary widely based on regional economic conditions. Urban areas with higher living costs often have increased wage rates for skilled laborers, thereby elevating overall project costs.
In contrast, rural areas might offer lower labor costs due to a smaller demand for high-wage skilled work.
Transportation and shipping expenses can further exacerbate regional pricing differences. Areas that are distant from manufacturing hubs or distribution centers might incur higher costs for delivering materials to the job site.
For instance, transporting oak flooring to remote or less accessible locations can add a significant surcharge, impacting the project’s total cost.
Finally, local building codes and permitting fees can affect the cost of installation projects. Some regions may have stringent regulatory requirements that necessitate additional inspections or approvals, contributing to higher labor costs.
Understanding these regional variances is crucial for effective planning and budgeting of oak flooring projects. Homeowners should take the time to research local conditions and seek multiple quotes to ensure a financially sound investment.
8. Manufacturer and Brand
Brand reputation significantly influences the pricing of oak flooring. Established brands with a long history of quality and durability often command higher prices compared to lesser-known manufacturers.
Consumers tend to associate well-known brands with reliability, warranties, and superior customer service, making them willing to pay a premium.
This trust and perceived value allow renowned brands to maintain higher price points, even if the actual cost of production is similar to that of lesser-known competitors.
The cost of oak flooring can vary widely between different manufacturers. Factors such as production methods, sourcing of raw materials, and scale of operations contribute to these disparities.
For example, manufacturers operating on a large scale may benefit from economies of scale, enabling them to offer lower prices. In contrast, boutique or smaller manufacturers might emphasize artisanal quality and unique finishes, which can drive up costs.
Additionally, manufacturers that invest heavily in sustainable practices may also have higher prices due to the premium for eco-friendly materials and processes.
Consequently, homeowners need to compare prices and consider the specific benefits offered by different brands and manufacturers when selecting oak flooring.
9. Environmental Considerations
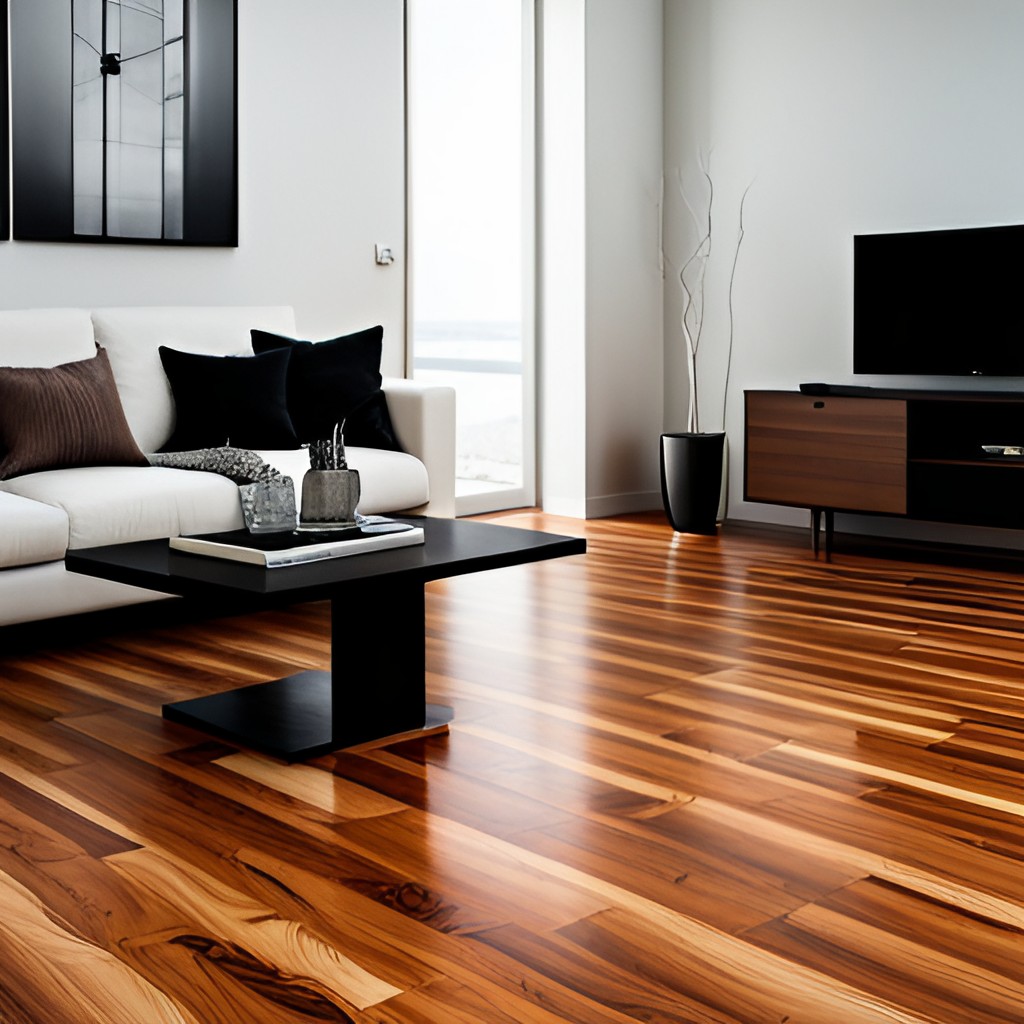
The source of the oak wood significantly affects the cost of oak flooring. Oak sourced from sustainable forests, where trees are responsibly harvested and replanted, often comes at a premium.
This premium supports sustainable forestry initiatives, ensuring that oak forests are managed in a way that maintains the ecosystem and biodiversity. Additionally, the geographical location from where the oak is sourced plays a crucial role.
For instance, oak harvested locally might be less expensive due to reduced transportation costs, whereas exotic or imported oak can be more costly due to shipping and import taxes.
Sustainability Factors
Sustainability practices also contribute to the overall pricing of oak flooring. Manufacturers that prioritize eco-friendly techniques, such as using low-emission adhesives and finishes or employing energy-efficient production processes, may have higher costs.
These practices, while beneficial for the environment, require investment and innovation, which are often reflected in the final product’s price.
Certifications such as the Forest Stewardship Council (FSC) label or other eco-certifications can also influence pricing.
Products bearing these certifications are typically more expensive, as they assure consumers of the product’s sustainability and environmentally responsible production.
Impact of Eco-Friendly Options on Price
Eco-friendly options impact the price of oak flooring in several ways. First, the use of sustainable materials and practices usually increases production costs, leading to higher retail prices.
Consumers, however, may be willing to pay this premium due to the growing awareness and demand for environmentally responsible products. Secondly, the long-term benefits of choosing eco-friendly options include not only a lower environmental footprint but often better indoor air quality and durability.
These benefits can justify the higher initial investment for many homeowners.
Lastly, government incentives or rebates for sustainable home improvements can sometimes offset the higher purchase price, making eco-friendly oak flooring a more viable option.
Conclusion
In summary, the cost of oak flooring is influenced by a variety of factors including the type and grade of oak, plank size, finish options, and installation methods. Each of these factors contributes to the overall expense and can vary depending on regional price variations and the reputation of the manufacturer or brand.
Additionally, environmental considerations such as sustainable sourcing and eco-friendly practices play a significant role in determining the price.
By understanding these 11 comprehensive factors, homeowners can make informed decisions that align with their budget, aesthetic preferences, and long-term needs, ensuring they achieve both beauty and functionality in their flooring choices.
FAQs
How can I tell if oak flooring is sustainably sourced?
To determine if oak flooring is sustainably sourced, look for certifications such as the Forest Stewardship Council (FSC) or the Programme for the Endorsement of Forest Certification (PEFC). These labels ensure that the wood comes from responsibly managed forests.
Is eco-friendly oak flooring more durable than standard options?
Eco-friendly oak flooring often boasts greater durability due to higher-quality materials and rigorous manufacturing standards. Additionally, natural finishes used in eco-friendly options can help protect the wood and enhance its lifespan.
Are there any financial incentives for choosing eco-friendly oak flooring?
Yes, some governments and local authorities offer financial incentives, such as tax rebates or grants, for sustainable home improvements including eco-friendly flooring. Check with local agencies to see if you qualify for any available programs.